Powder coating electrostatic spraying method, thermal spraying method, suction method, fluidized bed method, roller coating method, etc. The inner coating of the pipeline generally adopts the friction electrostatic spraying method, the suction method or the thermal spraying method; the outer coating of the pipeline generally adopts the electrostatic spraying method; the special-shaped parts adopts the fluidized bed method or the electrostatic spraying method.
These spraying methods have a common feature, that is, the workpiece needs to be preheated to a certain temperature before spraying, so that the powder will melt as soon as it comes into contact, and the residual heat should enable the coating film to continue to flow, further leveling and covering the entire surface of the steel pipe, especially In the depressions on the surface of the steel pipe, as well as on both sides of the weld, the molten coating flows into and fills, so that the coating is closely combined with the steel pipe, minimizes the pores, and solidifies within a specified time, and finally terminates the solidification process by cooling with water.
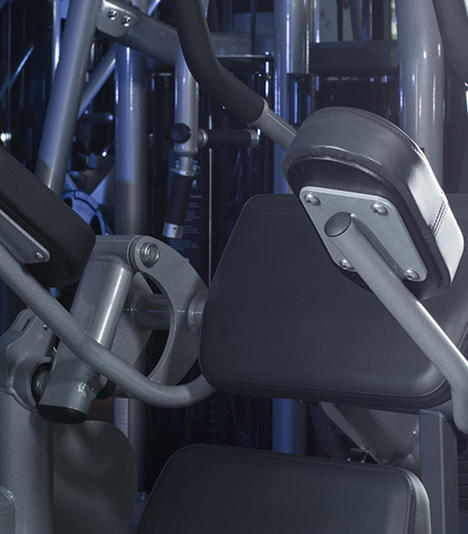
Although the underground does not contain extremely strong corrosive chemicals, the buried pipelines are exposed to salty groundwater, various organic acids produced by microorganisms in the soil, and stray currents, which will produce electrochemical reactions and corrode. It is well known that the three elements of electrochemical corrosion are: water, oxygen and ions. Both epoxy and polyethylene coatings are high polymer films, which can block the penetration of the above three factors to varying degrees and play an anti-corrosion role. However, due to the difference in molecular structure, the two coatings have their own advantages and disadvantages.
Due to the characteristics of good pressure bearing effect and high aging resistance, the main lines of water supply and gas supply pipelines generally use large-diameter steel pipes, which raises the anti-corrosion of steel pipes to a higher level. It can be said that the quality of anti-corrosion determines the use of pipelines. life. The corrosion of buried steel pipes has always been a problem. Before the 20th century, the anti-corrosion coatings used were mainly coal tar and asphalt, and later hot-pressed polyethylene tapes appeared. These materials have been proved to be effective in use. However, due to environmental pollution, low application efficiency, poor adaptability and other reasons, the use of these materials has been limited. It was not until the emergence of sintered epoxy powder coating after the 1950s that revolutionized the corrosion resistance of steel pipes, and sintered epoxy powder Used in conjunction with polyethylene coating, the level of pipeline anti-corrosion has reached an unprecedented level, which is a relatively combined anti-corrosion method.
Polyethylene PE powder for pipeline engineering is a thermoplastic powder coating based on non-polar low density and linear low density polyethylene (remelting), which has a history earlier than fusion-bonded epoxy powder coatings. Because its molecule is a non-polar molecule and does not have active functional groups, its adhesion is poor. This fatal shortcoming limits its development. Later, the development of graft modification technology made polyethylene molecules have some polar groups and adhesion. It has been improved, but it is still far from the bonding strength of the fusion-bonded epoxy powder coating coating and steel. However, polyethylene has super toughness and impact resistance, as well as water resistance and edge coverage, and is very suitable for coating some outer-coated or sharp-edged workpieces. However, due to adhesion reasons, it is generally not recommended for inner painted.
Fusion-bonded epoxy powder is a thermosetting powder coating based on epoxy resin (heating and melting, then solidifying into a film, and no longer being melted by heat), it has been used in the field of pipeline anti-corrosion for more than 50 years, and it was the earliest in service. The anti-corrosion pipeline of the epoxy powder coating coating is still in play. Fusion-bonded epoxy powder coating is a solid coating that is transported and dispersed with air as a carrier. It is applied to the surface of preheated steel products, melted, leveled and cured to form a uniform coating. Name, English name Fusion Bonding Epoxy Powder Coatings, referred to as FBE.
Each particle of the fusion-bonded epoxy powder contains all the constituent components uniformly, resulting in a continuous and stable uniformity of the coating operation and the resulting coating. Its physical properties, chemical properties, performance, durability, safety and environmental performance, economy (thin coating, only 300~500 nm, low cost) are generally recognized by the anti-corrosion industry, and can stand the test of practice and time. It is used in water, oil, gas and other aspects, and plays a unique role. After decades of continuous development and improvement, this technology has become mature. It has performances in different pipe diameters, transmission media, connection methods, and geographical environments. Because the epoxy resin molecule has more than two active functional groups (hydroxyl group and epoxy group), it forms a three-dimensional network molecular structure after curing, and can chemically react with the steel surface to form chemical bonds, so it has excellent adhesion and rigidity. .